At Aerosint we developed a technology called Selective Powder Deposition (SPD) recoating. This technology allows the user to make 2D patterns with multiple powders. We are known for having integrated our SPD recoater in a Laser Powder Bed Fusion printer from Aconity GmbH. This made it the first commercial LPBF printer with multi-material printing capabilities.
Another area where we see a lot of potential for SPD is in powder metallurgy. SPD recoating combined with direct pressure-assisted sintering has the potential to make very unique parts. It is another field we have been experimenting with for a while now.
This approach uses a high-temperature resistant die as used in Hot Pressing or Electric current based sintering methods such as SPS, FAST and PECS. Using our technology the powder is deposited directly into the die without the need of an excess material. Using the bottom punch of the die as a building platform a complex 3D powder structure can be constructed using the materials of your choice. Indeed, one of the strengths of SPD technology is the broad range of compatible materials, ranging from most metals in fine powder form as used in additive manufacturing and powder metallurgy, spray-dried ceramics, polymers, and more.
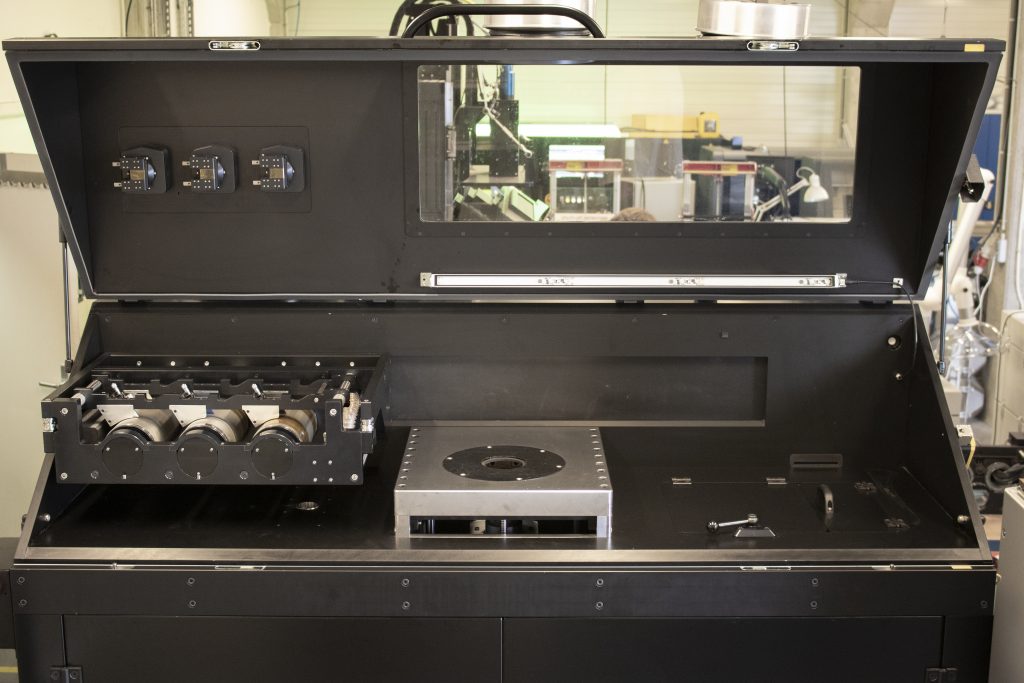
The process to fill the dies follow 4 simple steps :
- Mounting the die and bottom punch and aligning it with the deposition head
- Sequential deposition of patterned layers
- Inserting the top punch and lowering the deposit
- Pre-compaction in a press to fix the powder in place
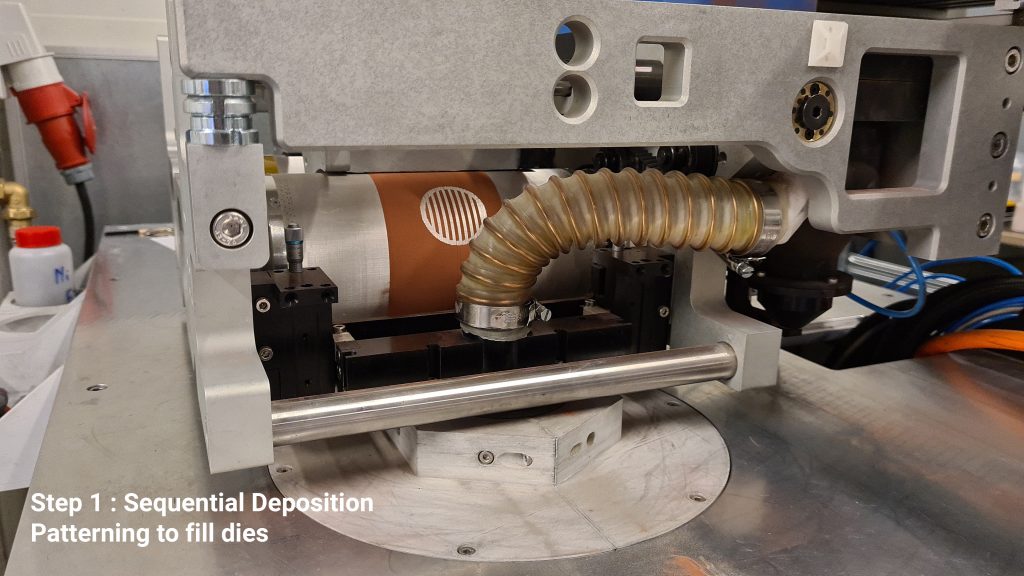
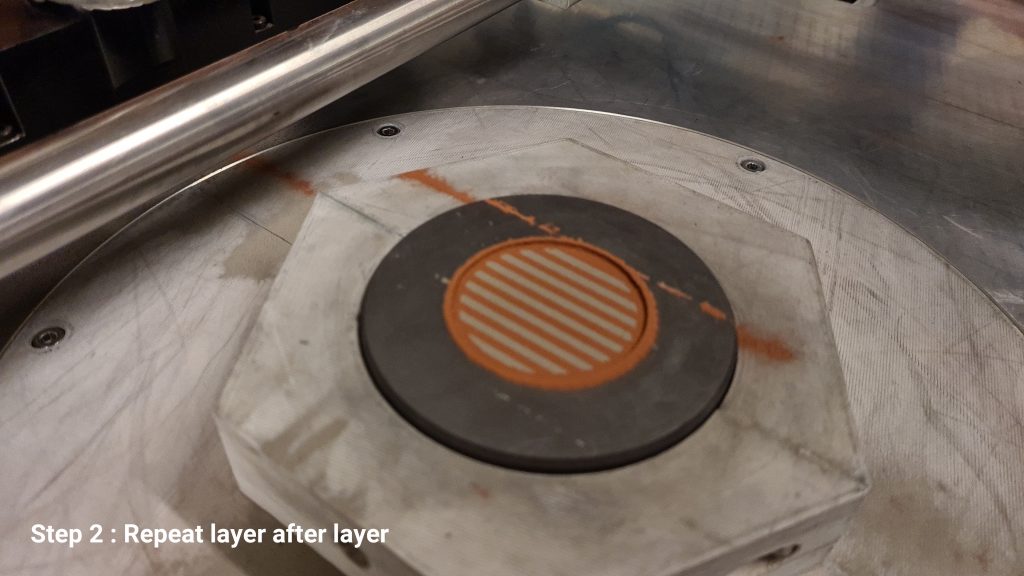
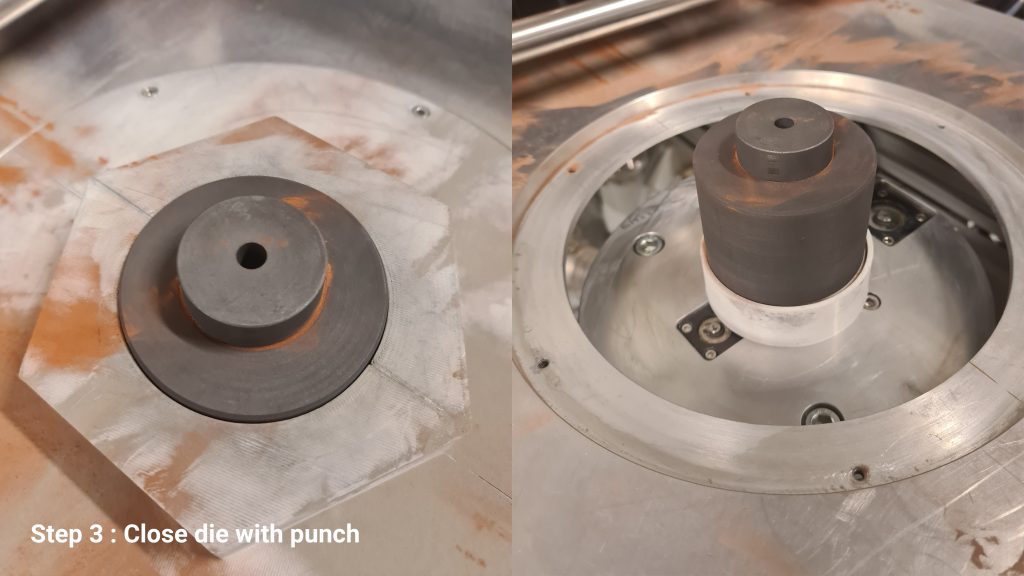
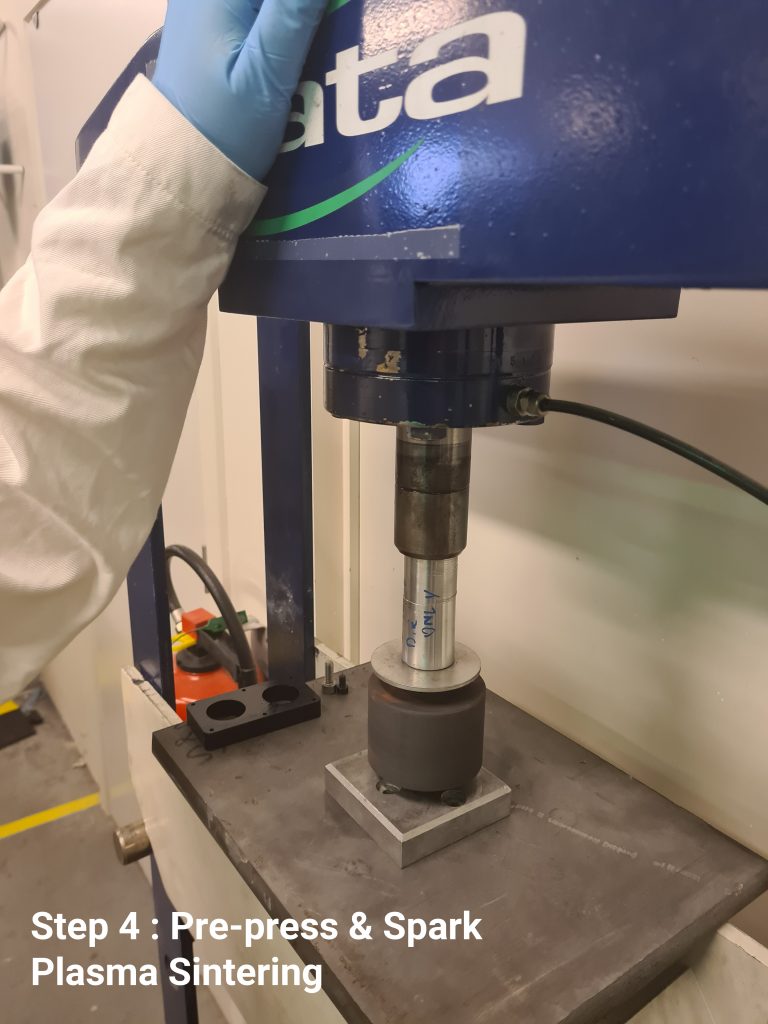
After these 4 steps, the powder is ready for sintering. Due to the precompaction the powder is firmly fixed in place, facilitating transport.
The materials that can be combined are subject to compatibility during sintering. This requires an overlap in the sintering windows, the pressure and temperature at which the individual materials densify, and a match in thermal expansion properties. While the latter might sound challenging, functional gradients and simulation-driven design can be used to compensate for small mismatches, even allowing co-firing of select pairs of metals with insulating oxide ceramics.