Luckily a simple solution to this economical and ecological non-sense exists.
Today, 2 years after releasing our first generation powder coater, we are launching our second generation of powder coaters that exist in a 3-material configuration. Adding a third material in the process greatly improves powder coating well beyond just the possibility to print multi-material. This article describes why.
Adding a third material to the process to achieve no waste
Rather than trying to recycle mixed powders, our preferred strategy to solve this problem is to avoid material waste in the first place. This is accomplished by adding a third material to the process that we call the “filler material”.
The filler material, as compared to the two “functional materials”, will not be fused or incorporated into the part. The filler material is deposited to literally “fill” the powder bed with powder.
At the end of the printing process, all the filler material is recovered and re-used in the next build job preventing any kind of waste. Even if the filler material gets contaminated by a bit of non-fused functional metal powder, this will not be an issue because the filler material will only be reused as filler material. A filler material is never reused as a functional material.
Problem solved: ✓

Simple and elegant solutions usually lead to a number of follow up questions which we address below. There is also much more to say about the use of a filler material for powder bed printing. We are convinced that using a filler material has the potential to completely disrupt conventional powder recoating.
Why would you continue to fill your entire powder bed with expensive powder if you can use a cheap and reusable filler material, even for single material printing?
What type of powder should you use as filler material ?
The easy choice is to use discarded metal powders you are printing with. Or even a mix of it. You don’t have to worry about the powder not being adequate for printing because this powder will not be incorporated into your parts.
But what about choosing a filler material of a completely different nature?
Use a cheap filler material
One of the smartest choices in our opinion is to use an inexpensive ceramic powder as a filler material. This strategy is particularly interesting when you print with expensive metal powders. Like medically certified powders or even precious metals. For those powders, every gram you put in the system matters… Let’s take gold powder as an (extreme) example. 1 kilo of gold trades at more than 50.000 €. With the filler material strategy, you would only load 10%-15% of gold powder in the process, corresponding to the quantity which is transformed into a part. All the rest of the powder bed can be filled with a cheap ceramic powder that is up to 10000 times cheaper than gold powder.
Another example where this strategy is particularly effective are for large scale industrial printers. Printers are getting bigger and bigger. This also means the quantity of powder you have to load into the system is growing significanlty. Who likes to immobilise hundreds of thousands of euros worth of raw materials in a machine and accept all the risks associated with it? The filler material again brings a solution to this inefficiency.
Use a functional filler material
We also think there is potential in selecting the filler material to have a specific property. For example, you can select a filler material that is soluble. The soluble filler material might greatly facilitate the cleaning of parts with complex geometries or small channels. You could also select a filler material that has a particularly high flowability and low weight. This will facilitate the depowdering of your parts and potentially make the automation of this task much easier.
What will the powder recycling rate be with this approach ?
It will be close to 100%.
Thanks to our digital powder printing approach you don’t actually deposit more functional material than you need to print your parts with. Indeed, the Aerosint coater doesn’t need to drag a big volume of powder from one side of the printer over the powder bed to an overflow bin like traditional roller or blade coaters. Our powder deposition process is a digital on/off process. Like an inkjet nozzle we only deposit powder where we want to print.
As mentioned earlier, all the unfused powder from the powder bed (mostly filler material) can be recovered and reused as filler material in the next print job. As such you achieve close to 100% powder recycling.
Our powder coater revolutionizes powder recoating like digital 2D printing revolutionized mask printing decades ago. When you think about it, it’s nonsense that you have to fill a powder bed with a lot of powder and only end up transforming 15%-20% of it into a part (considering the average industrial packing density in powder bed AM).
Even if machine manufacturers claim you can re-use 100% of the unfused powder, in practice, you inevitably end-up wasting material while you clean your machine or transfer the powder from one bin to another. With Aerosint’s recoater you will still waste this bit of powder but it will be the inexpensive filler material, not your expensive functional metal powder…
So essentially this means you always print parts using virgin material ?
Exactly! Goodbye the time that you have to worry about mixing your previously used metal powder with virgin material and make sure the powder stays within certain material specifications. Even if this powder recycling process is today industrialized and well-controlled by a lot of end-users, by only depositing the amount of virgin metal powder you need to print your part with, you can completely get rid of this resources consuming hassle.
Having the possibility to only work with 100% virgin material makes it also much easier to have a stable and reproducible process because your powder will always have the specifications guaranteed by your powder supplier.
This advantage is particularly valuable for very demanding industries and applications like in medical and aerospace.
When are you releasing the 3 materials recoater ?
The 3-material coater is today available for pre-order. The first commercial system that this coater can be used with is the Aconity MIDI+. All Aconity MIDI+ printers are compatible with the 3-material coater. The coater can be acquired also in a 2-materials configuration or as a stand-alone product for custom machine integrations.
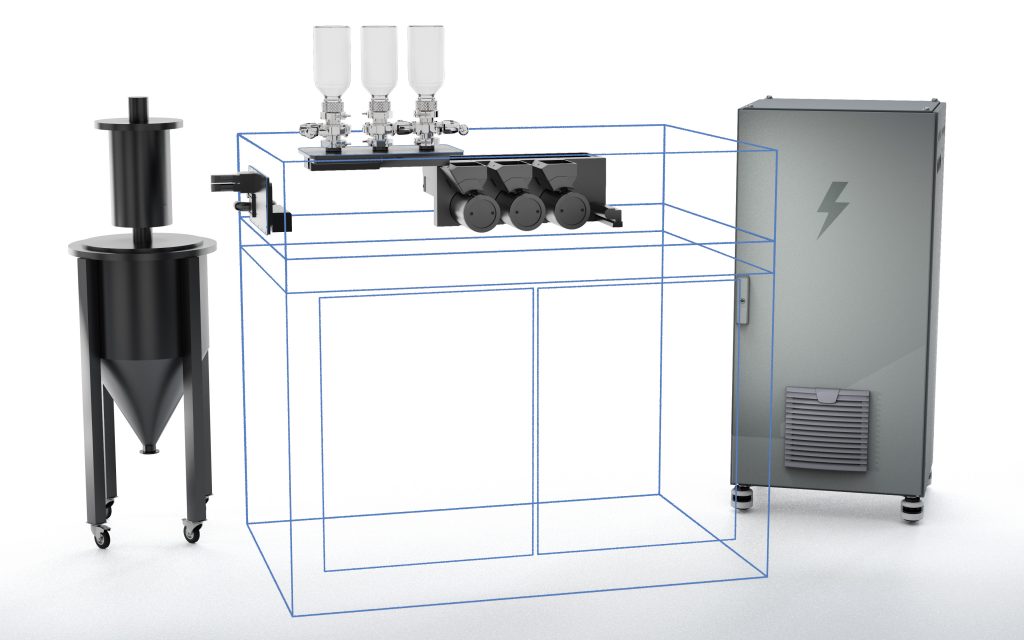
To learn more about the 3-material coater make sure you reach out through our contact page or via email at info@aerosint.com.
What are future releases going to include ?
There are a few areas of development for the Aerosint powder coater. The main ones are:
- improving the speed of the recoating process,
- improving the powder pixel resolution,
- scale the dimensions of the powder recoating area.
Each of those key developments will increase Aerosint’s addressable market within and beyond LPBF. Digital powder recoating use cases also spans beyond AM. We are working on multi-material powder metallurgy applications but also in other unrelated industries.
We are strongly convinced that digital powder coating has the potential to be faster, lead to higher material efficiency, and be more versatile for multi-material but also for single material printing. As such, we believe digital powder coating could become the preferred method for a number of powder based AM processes in the future.