Security is increasingly vital as 3D printing scales. Aerosint offers powder bed printing with multiple materials which can extend InfraTrac’s chemical security into powder bed fusion printing processes.
Until now, InfraTrac’s innovative taggant approach had not been possible in powder bed additive manufacturing processes, due to the process single material coating limitations. Aerosint’s selective powder deposition coater brings a solution to this.
In a first step, Aerosint is producing simple demonstrator parts from polymer and metal that include “fingerprinting” sites based on a powder formulation developed by InfraTrac, which will then test and verify the parts. This collaboration forms the basis for simple, robust, and scalable part authentication for industries in which strict quality control is critical.
The security of 3D printing is a concern
As 3D printing matures, it portends long-term alterations in manufacturing, outsourcing, and inventory management. Light, complex, customizable products can be made in new ways, of new materials, in new places by new players. In the emerging distributed manufacturing model, spare parts can be generated as needed and where needed.
Multiple transformations lie ahead: products can be made more fixable, less inventory needs to be created, stored and protected, less shipping will be needed, there will be less waste, and no borders complicate trade if you can send a file instead of a physical good. All of those advances have other implications, however, and the ability for anyone to create end-use parts enables bad actors as well as helpful new outsourcing players. Some of the people 3D-printing aircraft and auto parts are not going to be licensed, careful, high-quality suppliers, and new approaches to protection will be required.
In this new model, a digital file contains the information to create a product. Software protections and digital rights management are necessary to protect the intellectual property in that file. However, none of those digital protections are going to keep us safe from 3D-printed counterfeit parts and products: once the print is complete, its digital safeguards lose their power. Anti-counterfeiting for additive manufacturing needs to be integral to the final printed product.
A solution to 3D printing counterfeiting
Standard approaches to brand protection have included overt, covert, and forensic techniques. Overt protections reassure the consumer that the football jersey with the hologram tag is likely to be authorized and authentic… but they telegraph to the counterfeiter exactly what to spoof, so those holograms, alas, are no longer trustworthy; you can buy your own on rogue marketplaces. Covert protections have the advantage of working behind the scenes. The advent of 3D scanners expands what can be “seen” and replicated, so that, for example, laser etching or tiny barcodes are no longer reliably covert. Forensic measures have historically required expensive lab equipment manipulated by expensive experts, but recent advances in photonics have enabled an explosion of new portable, easy-to-use instruments that put forensic-quality science in the hands of field personnel, with near-instant authentication capability.
Process disruption and technology adoption. Complexity is the enemy of security: difficult procedures invite work-arounds. That’s what makes us reuse passwords even when we know we shouldn’t. Security procedures that align with existing processes are most likely to be adopted, and less likely to be circumvented. Applying taggant or codes should be part of the standard print or manufacturing workflow, not an add-on. Detection should take seconds, with inexpensive, portable, off-the-shelf equipment.
Scalable solutions. InfraTrac’s tagging model uses commodity taggants for scalability. Optimally, taggant is placed during printing, in a small subsurface spot. Selecting a single, highly-detectable taggant and dispersing it throughout the product (in filament, or mixed into pellets or powders) seems like a good idea, but putting taggant everywhere makes it easier for counterfeiters to find it and copy it. Instead, InfraTrac uses compatible chemicals as taggants, as part of the print process, and hides them in a small covert spot for additional deterrence.
This compatible-chemical approach gives InfraTrac millions of taggant combinations, with open supply chain options, but it does rely on a multimaterial print process. Until now, powder bed printing was a problem: clearly important for scalable industrial applications, but limited to single materials.
Selective powder deposition to integrate Infratrac’s security taggants in 3D printed parts
Laser powder bed fusion (LPBF) methods such as selective laser sintering (SLS) and selective laser melting (SLM) build parts through the selective fusion of powdered material spread in thin layers over a build surface. Currently SLS and SLM systems spread powder in thin layers through rollers or doctor blades, and neither offer the flexibility to place multiple powders at specific locations within a build layer. True multi-material LPBF requires a system for precise placement of two or more powdered materials within one layer. This “voxel-level control” forms the basis for the selective powder deposition system that Aerosint is developing. Metal or polymer components built using an SLS/SLM system equipped with Aerosint’s recoater can contain InfraTrac-traceable materials embedded at specific sites within the part. As these taggant materials can be made visually identical to the part’s bulk material, counterfeiting is virtually impossible and part sourcing authenticity can be ensured to the highest degree of confidence.
About InfraTrac
InfraTrac (Silver Spring, Maryland, USA) provides chemical security for additive manufacturing, printing taggant right into the part, with instant field detection.
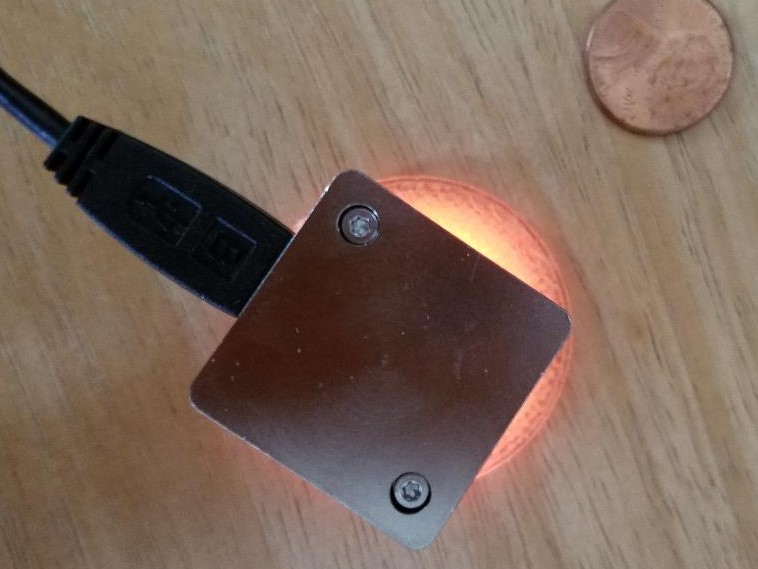
Read more about InfraTrac’s security solution in the latest 3D Printing Industry post.