Ceramics are hard – and not just mechanically speaking! Compared with metals and polymers, ceramic materials are incredibly difficult to shape through subtractive forming methods like machining, thanks to their inherent mechanical hardness and brittleness. This is why 3D printing of ceramics is very enticing to the industry at large. 3D printing (or additive manufacturing, AM) of ceramic components should theoretically allow for nearly unlimited freedom in choosing part geometry. Despite this incentive the additive manufacturing of ceramics is lagging behind the printing of metals and polymers, and all current ceramic AM methods have process-related limitations on part wall thickness, and thus limitations in their real-world usability. In this article we delve into the reasons for this and suggest how Aerosint’s selective powder deposition technology might represent a breakthrough solution for ceramics processing.
Why are ceramic parts hard to produce in the first place?
Simply put, ceramics don’t have the right material properties needed for successful machining, casting, or injection molding – the three most common industrial processes for forming useful parts from raw materials. Ceramics are brittle and melt at much higher temperatures than most metals and all polymers. They also are sensitive to thermal shock, cracking when they are cooled down fast from a molten state. Unlike polymers, ceramics cannot be “cross-linked” from a liquid precursor solution. This also means that small quantities of ceramic material cannot be added by melting, welding or reaction onto an existing structure. Ceramic parts are instead made by forming a shape from powdered material followed by consolidation at high temperature, sometimes aided by high pressures. This process of fusing particles together driven by thermal energy is known as “sintering”.
For most applications sintering must be carried through until virtually no porosity is present to meet the mechanical properties for which technical ceramics are known for. Even one percent by volume of finely distributed porosity or a single individual large pore can cause premature failure of parts. This cannot be tolerated in critical parts, especially since failures are often catastrophic.

How does one make a ceramic part traditionally?
Traditionally ceramic particle and polymer slurries are cast or injection molded to create a shaped “green body”, a fragile object composed of yet to be fused particles that has the shape of the final ceramic part. As dry ceramic particles don’t just readily stick together at normal temperatures this forming process often needs some help. It’s for this reason that many ceramic part forming processes, including all current commercial ceramic AM processes, employ polymer binders (effectively glues) to act as a stabilizer for ceramic powder shape. Depending on the amount of binder this can mean that the green body has mechanical properties ranging from chalk to polymer-like. To achieve the final ceramic properties the powder particles must first be fused together via sintering. Before this is possible any polymer present in the green body must be removed.
During a de-binding step, the green body is heated to allow polymer to break down into smaller gaseous molecules and diffuse out of the piece. After debinding, the part is subject to a true sintering cycle during which atomic diffusion between ceramic particle contact surfaces leads to consolidation and densification, all at a few hundred of degrees lower than the true melting point of the ceramic. Finally, after this sintering step the part is truly a ceramic and no longer has polymer or chalk-like properties.
They do sinter parts from powder in AM. Can’t we do the same with ceramics?
Indeed, in selective laser sintering (SLS) a high power laser is used to locally fuse polymer, and to a lesser extent metal, particles together, gradually building a structure layer by layer by scanning the laserspot over the powder bed. The highly concentrated energy input by the laser means that the material is heated and cooled extremely rapidly, and that a hot spot moves through the part during processing.
Unfortunately due to the high sintering temperature needed for ceramics both thermal differences would be even more extreme. And though ceramics are typically used as high temperature resistant materials, they tend to be thermal shock sensitive, not liking fast temperature changes. As such they do not lend themselves to localized laser sintering.
Instead all current commercial AM technologies for the fabrication of ceramic parts is based on the use of a polymer binder, either polymerized in situ using stereolithography or applied using a jetting / printing, which brings us back to the issue of debinding. Polymers can often be dissolved in organic solvents or burned out, so why are binders problematic? There are two main reasons: part stability and processing time. Burning out binders causes polymers to be decomposed into gases, and at high temperatures gas bubbles trapped within small pores can stress parts to the point of cracking.
Even in the best case scenario where no cracking occurs, full part densification occurs only if most of the polymer degradation products can nearly completely diffuse out of the small pore structure of the ceramic before the pores collapse. Given that diffusion time increases by a factor of four when part thickness is doubled, the time required to ensure full debinding of thick-walled parts simply becomes too long to be practical. Instead most current ceramic AM technology focuses on thin, delicate, small parts.
If not using lasers, how is 3D printing of ceramics already done?
As mentioned, direct consolidation of ceramics with laser-based heating results in parts that crack easily, so a ceramics-based SLS analogue is not realistic. Rather, the AM techniques developed for ceramics were logically based on slurry-based casting and molding techniques (followed of course by debinding and sintering) used for many decades.
The first freeforming method to be called “3D printing” was effectively printing ceramic green parts; it used an inkjet printer head to spray a binder fluid onto successive flat layers of powder. This technique was developed foremost to print full color models using gypsum powder, without the intention to sinter or densify them afterward. The printed figures are not intended as structural parts.
This “binder jetting” process is currently also used with powders of harder and more industrially useful ceramics. The challenge here is to maximize the powder bed density and uniformity while minimizing the volume of liquid binder needed for sufficiently strong green parts. Binder jetting has the advantage of being a rather scalable process with the possibility of producing hundreds or even thousands of green parts in a single build. It suffers from the disadvantage of low green part strength and low surface finish quality. And of course, it still uses a binder material.
Another, more recently developed method involves using slurries composed of ceramic particles suspended in liquid polymer resin in a stereolithography process. In stereolithography, layers of photosensitive thermoset resin are successively crosslinked with ultraviolet light in order to form a piece. The crosslinking process transforms the liquid resin into a solid material and at the same time immobilizes the suspended ceramic particles. This crosslinking method is also one of the limitations. In order to polymerize the resin the concentration of particles should be low enough as not to block the UV light and the used particles should not be UV reactive. A low concentration also reduces slurry viscosity, aiding the flow of resin around the printed object.
This technique has the advantage of very small feature size and high quality surface finish, but of course the binder polymer must still be burned out and thus part thickness and size is limited. The diminutive size of the printed objects is in part also an effect of debinding. As a lot of material is evaporated during debinding, causing substantial shrinkage and an effective part size that is only a fraction of the stereolithography print volume. The cost of the resin materials and the lack of scalability (and thus higher cost) are some of the disadvantages of the process.

Other commercial AM technologies for technical ceramics are on the market, but they all have the use of significant quantities of polymer binder in common. In XJet’s nanoparticle jetting slurries of resin and ceramic nanoparticles are used in an inkjet and UV curing based approach, yielding green parts similar to those obtained via stereolithography. Rapidia uses water soluble polymer binders in their freeform casting process. And yours truly was involved in fusing ceramic loaded polymer particles together using SLS. The only binder free ceramic AM forming process to our knowledge is the freeform deposition using molten glass as demonstrated in academia.

So, if ceramic parts can already be made via AM, is there really a need for new technology or selective powder deposition?
Hopefully by now it’s clear why thick ceramic parts are difficult to produce with traditional polymer binder-based methods, including all current ceramic AM techniques. Still, these companies have found a market, so does anyone really even need or want thick ceramic parts? Yes, because in this case “thick” means having a wall thickness of five millimeters or greater; a thickness that in many industrial cases would still be considered quite thin. For many applications parts can be made stronger simply by adding bulk. Biomedical implants, manifolds for extreme fluid handling, dental prostheses, and investment casting cores are just a few of the applications for which thin, binder-free additive manufacturing would represent a sea of change.
In other applications, free-formed ceramics might outperform metals but are simply not used currently due to manufacturing difficulties. One simple example is bearings; ceramic bearings outperform their metallic counterparts in rolling and wear resistance, weight, rotation speeds, and operating temperature, yet they are many times the price thanks to their more expensive and time-consuming manufacturing process.
Is there then no other way?
Well, there might be. If we look at traditional ceramic production processes all one needs is a powder compact with a predefined shape. Aerosint is in the business of selective multimaterial powder deposition. With the Aerosint technology a powderbed can be built containing a predefined three-dimensional shape of technical ceramic powder surrounded by an inert support powder. It stands to reason that if the support powder sinters at a much higher temperature than the shaped build powder, a sintering temperature can be chosen that sinters only the build material together. In this way we might just have a winning solution for making near net ceramic shapes in a manner that more closely resembles the traditional production processes.
To explain it in another way, instead of using a mold to cast the particles in the form of a slurry, we deposit the mold together with the ceramic particles we want to sinter. As we do not need to remove water, and we choose a mold material that does not sinter, we can sinter the part directly. No debinding required, just put the entire powder bed into a furnace and start the heating cycle.
Of course, we could not resist trying this. For the parts shown below we used glass (low sintering temperature) and alumina (high sintering temperature), and lo and behold, we already got parts during the first try. And moreover, these parts are thick-walled. Our prototype setup does not yet have the resolution to obtain the same thin walled parts that are typical of the lithography processes. The limited resolution also results in a rougher surface texture than the parts obtained from technology that has been developed over the better part of a decade. Nonetheless the parts can be considered near net shape. And this is often sufficient for considering a production route as the need for machining surfaces is reduced to a minimum.
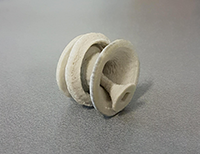

But still, with some elbow grease we will get better results, and get closer to the quality of stereolithograpy and binder jet parts without the debinding fuss. We promise first to show them here on Medium first, so be sure to follow us.
by Bram Neirinck and Kevin Eckes, Research Engineers at Aerosint
Are you interested to learn more about our approach to ceramics 3D printing? Or do you want us to evaluate if your ceramics applications can be printed with this approach? Let’s talk !