We can print!
In our previous articles we discussed some current limitations and issues with AM and explained how a new paradigm shift involving selective powder deposition could address these issues. Those with sharp eyes may have noticed that the results we showed were improved in each subsequent article! The purpose of this short update is to show you in a bit more depth what we’ve accomplished in the months since, including having printed several single-material 3D parts and several “2.5-D” (i.e. thin) multi-color and multi-material parts.
In our first article, we posted a GIF of a prototype powder deposition system we completed early in 2018 (below, left). We designed this system to be large and modular so that all mechanical elements were easy to access by hand and could be updated or modified as needed. Much of this past spring was spent doing iterative testing and making upgrades to the system that greatly improved the powder patterning quality.
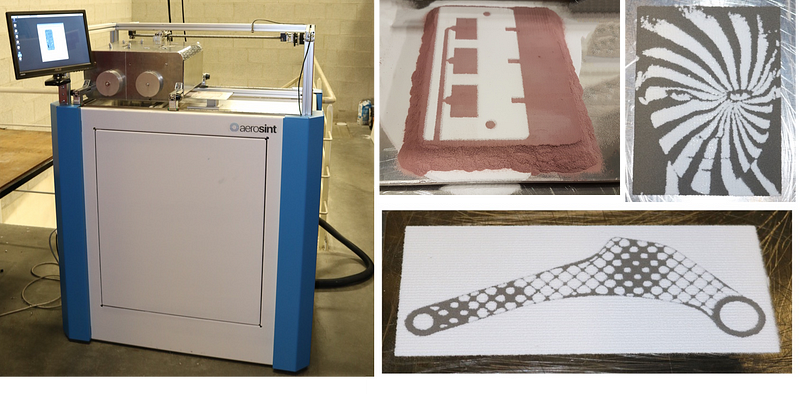
The knowledge we gained from this iterative process directly informed the design of a more compact powder deposition system to be integrated into an EOS P350 selective laser sintering (SLS) machine that we had acquired (below, left). We wanted to demonstrate how easily our system could fit in the normal SLS process and validate the powder savings and multi-material part creation opportunities through real-world testing. In the end miniaturizing our system to adapt to this machine with very limited space inside the build chamber was quite challenging, requiring significant modifications to the P350s normal structure to make space for all the required elements. During the summer we completed the design and manufacturing of the mechanical system (below, right). The as-conceived design was not without flaws; we needed to make a fairly major redesign of the infrared lamp assembly in order to prevent overheating of the assembly and supply powder in each roller. Several other as-designed elements also needed to be updated after testing, so this retrofit also became something of an iterative process.

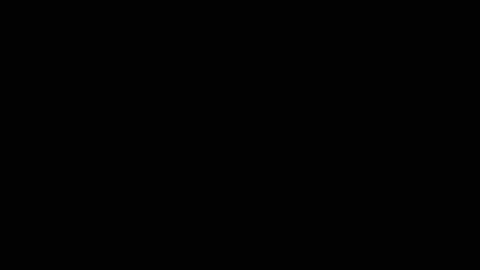
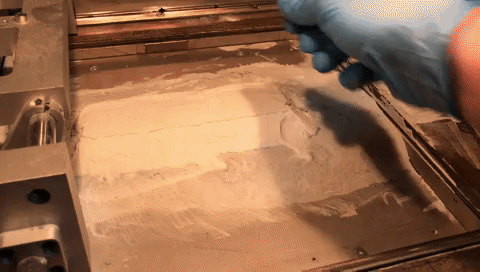
We were able to create some interesting pieces in a thermoplastic polyurethane (TPU) elastomer, without preheating, by patterning a non-fusing alumina (i.e. ceramic) support powder and sintering with infrared (IR)lamps. The results demonstrate as a first proof of concept the smallest feature size and positioning accuracy of our powder deposition process. With very little process optimization we were able to produce parts with real 3D features and contours, and we can see qualitatively how patterning separate build and support powders with different thermal characteristics allows for the near-elimination of build powder waste and nearly mess-free part recovery.
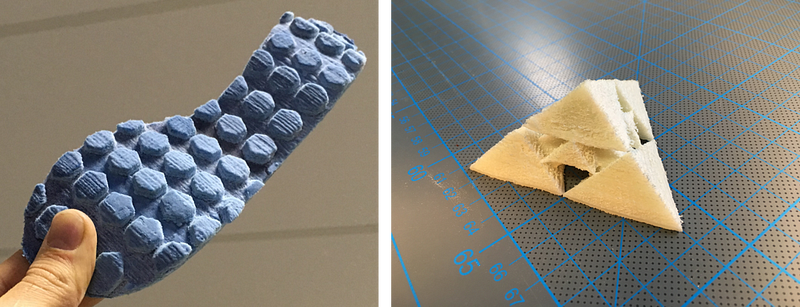
We could produce crude multi-color TPU parts as well, simply by tuning the concentration of the pigments added to the powders. When the pigment concentration in each powder gives the two powders roughly the same infrared light absorptivity, they fuse at about the same rate and result in multi-color parts with roughly uniform density (below, left). Co-sintering of an unmodified white TPU with a blue TPU was possible (below, right), however the blue TPU absorbed more light and thus the density of the blue areas was greater.
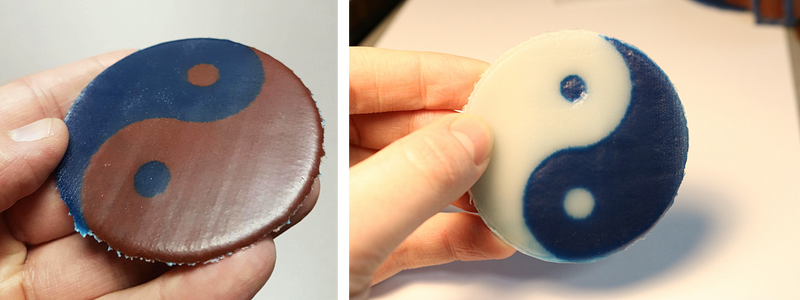
We managed to build thin parts with varying material composition in the X-Y plane; a nontrivial feat using powdered materials and IR light to sinter them. In the top left image in the figure below, rigid (but quite brittle) polystyrene was co-patterned and co-sintered with TPU (blue) with a gradient interface. We also co-processed flexible TPU (colored red in all other images in the figure below) with a rigid, non-warping polyamide (blue) with no preheating. Again, the pigment concentrations were roughly optimized so that for a given light exposure time the extent of sintering was similar for each material. In these images one can clearly see that the same force applied to the part causes significant deformation only in the red TPU, thus highlighting the different in stiffness between the red TPU and the blue PA material.
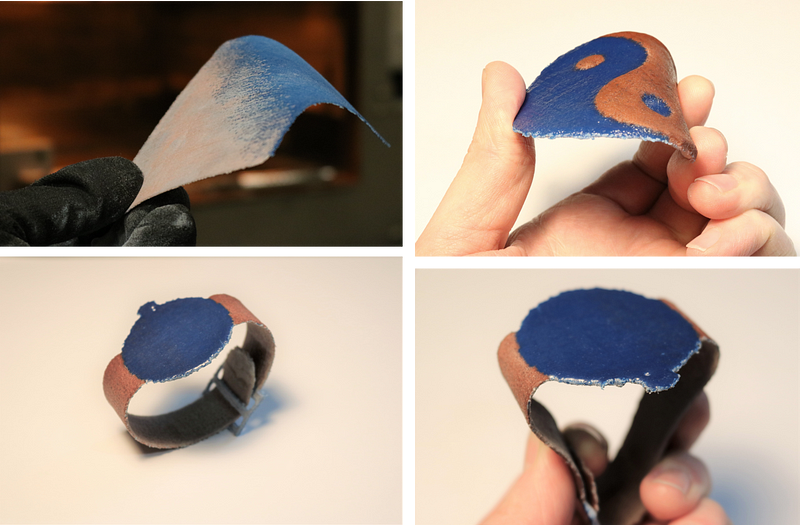
As far as we know, we are the first to demonstrate co-deposition and co-sintering of multi-colored polymer powders and powders of different chemical composition in the X-Y plane of a build. The results are rough and preliminary, but we hope to be able to greatly improve them in the coming months by exerting more control over the preheating and sintering process. Using a well-regulated preheating routine, we should be able to sinter rigid crystalline polymers such as polyamide-12, which tends to warp if the bed temperature is not held above its crystallization and below its melting temperature. We have been working to interface the hardware and software that control the Aerosint powder deposition technology with the laser scanning control hardware and software in the P350. With both preheating and laser control, results more similar in quality to normal SLS should be attainable, and beyond that we should be able to print multi-material parts composed of rigid, crystalline polymers and flexible, amorphous polymers, given that the materials’ processing temperatures are both roughly within the same range.
Of course, improving the sintering control doesn’t mean that we’re abandoning upgrades to the powder deposition system itself. We have a number of changes planned that should help us reduce the smallest feature size and increase the uniformity and reliability of the patterning process.
In the coming month we’ll also finish integrating a similar powder deposition system into a metal selective laser melting machine purchased recently by the AM Lab at the Fraunhofer IGCV in Augsburg, Germany. In a matter of a few short months, our clever engineers have adeptly designed and built a full two-material patterning system that should integrate seamlessly into the institute’s new machine. We hope to see some first results for multi-metal printing enabled by the Aerosint system in the first half of 2019. We are excited about these developments because our Fraunhofer collaborators have a great deal of experience in copper/steel laser co-processing and parameter development. With their help it will soon be possible to test a number of interesting and industrially useful multi-metal combinations to open up an entirely new range of applications for additive manufacturing.
Finally, a few weeks ago we had the privilege of exhibiting our recent progress at Formnext 2018, where we were selected as one of five winners of the Startup Challenge. Each winner was given a free booth space in the Start-up Area. This prize was a valuable opportunity that gave us useful visibility in the additive manufacturing industry, and we came away from the show with a strong sense of the excitement about multi-material industrial AM. There appears to be a real and growing market interest in multi-material, and it seems many of the major industry players are beginning to take notice of Aerosint’s technology and its potential role in advancing the capabilities of power bed AM.
by Kevin Eckes, Ph.D., R&D/Applications Engineer at Aerosint SA