Selective powder deposition can be utilized to furnace sinter intricate glass objects by using alumina beads as a non-fusible support powder.
How does it work?
In this binder-free process, the glass and alumina powders are selectively deposited layer by layer inside a die. The glass is deposited in the desired shape and the alumina is used to surround the glass and act as a support powder.
Step 1: Using Selective Powder Deposition to fill a die layer by layer with powder
The machine, designed and sold by Aerosint, clamps the die and moves down the die-punch for each layer. The powder deposition location inside the die is defined from a digital design file like with any other 3D printing process.

The steel die is filled with glass & alumina layer by layer using Aerosint’s Selective Powder Deposition printhead
Step 2: Transfer the die into the furnace & sinter
Once the object has been printed (still in powder form), the die filled with powder is transferred to the furnace. The furnace is heated to a high temperature, causing the glass particles to fuse together and form a solid object. The alumina support powder acts as a thermal insulator/diffuser. By shielding the glass powder from IR radiation from the heating elements the glass powder heats up very gradually, ensuring that the printed object does not deform or warp during the heating process. Using the alumina as a support powder allows the printing of overhangs or very intricate designs with no problem.
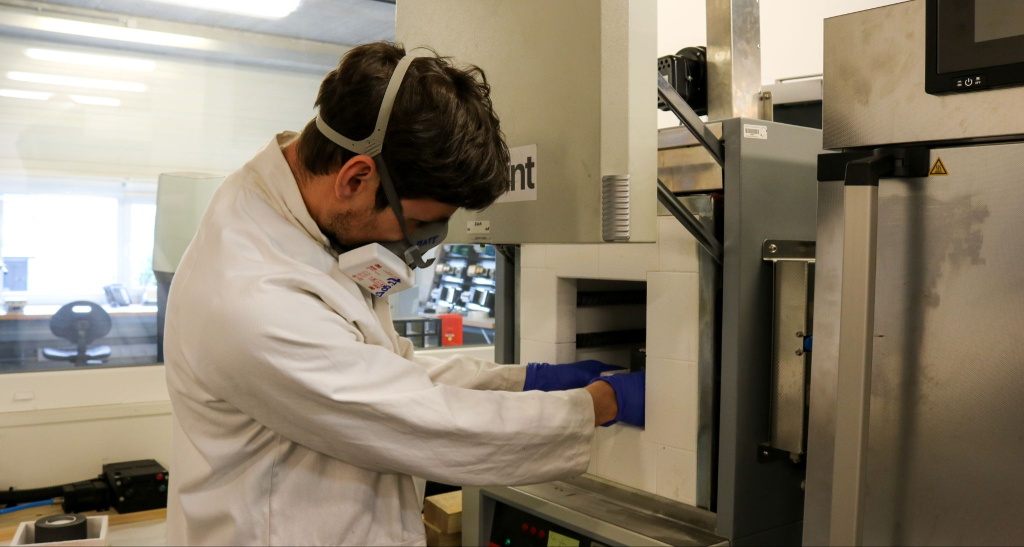
The steel die is placed in a furnace for sintering
Step 3: Depowder
The result is a dense glass part. The alumina support powder can be reused for multiple prints. The process is therefore very cost-efficient since it also doesn’t require any kind of additive or binder to work. Only the quantity of glass powder needed to print the object was consumed in the process.
Depowdering is done on a solid part limiting the risk of damaging it. It literally takes a couple of seconds!
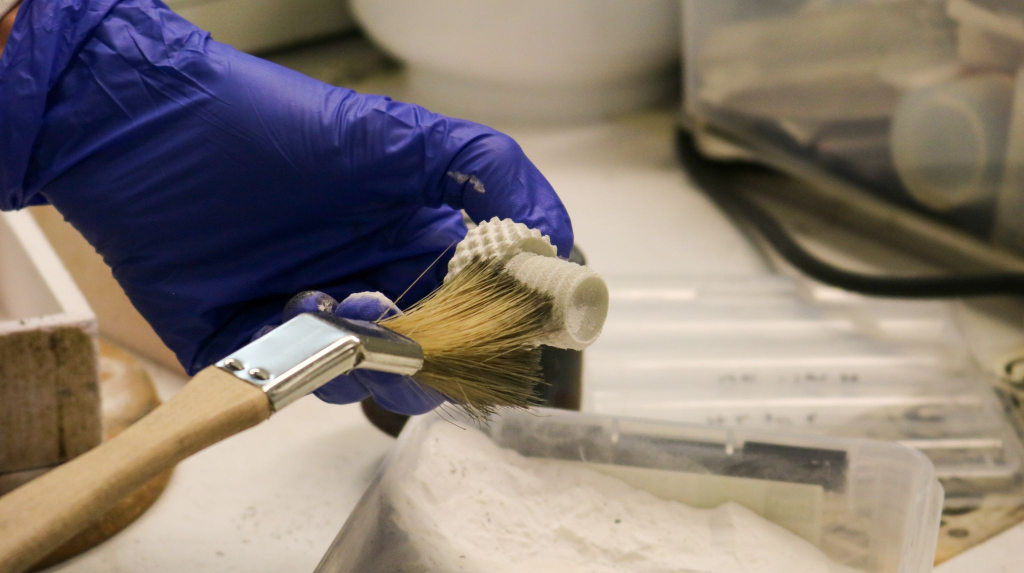
The sintered part is taken out of the alumina support powder
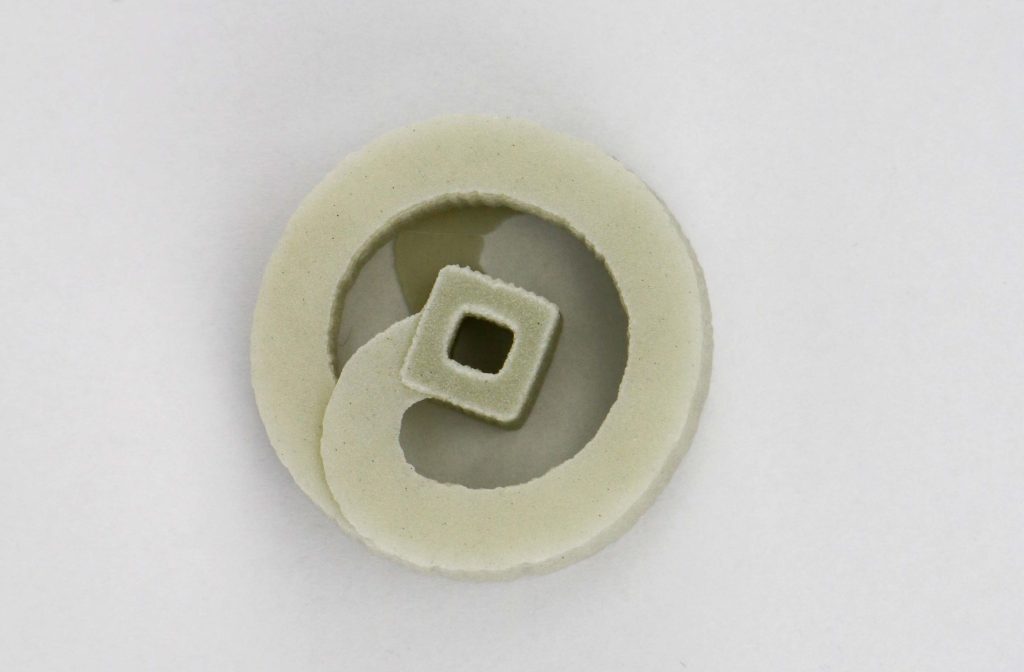
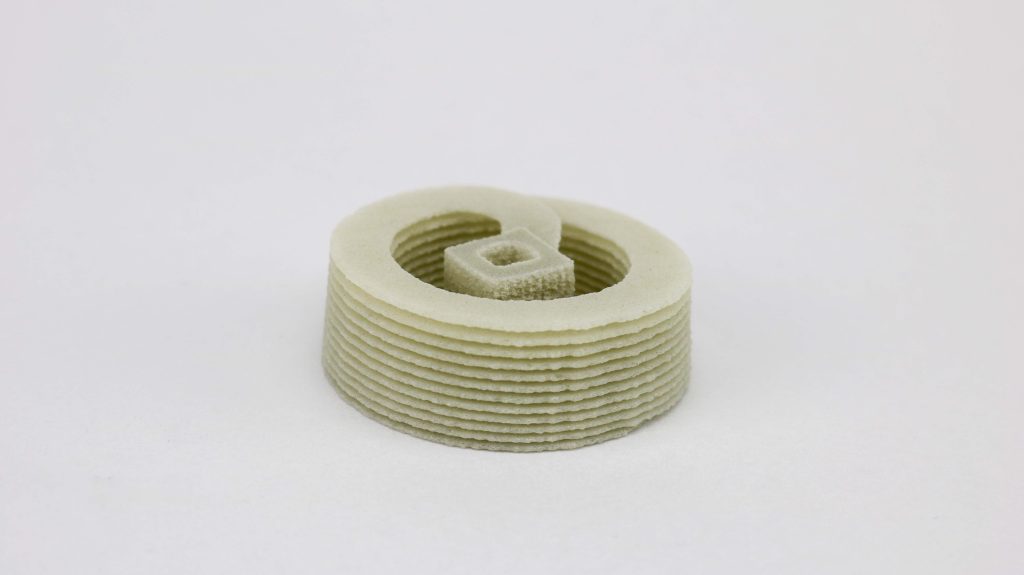
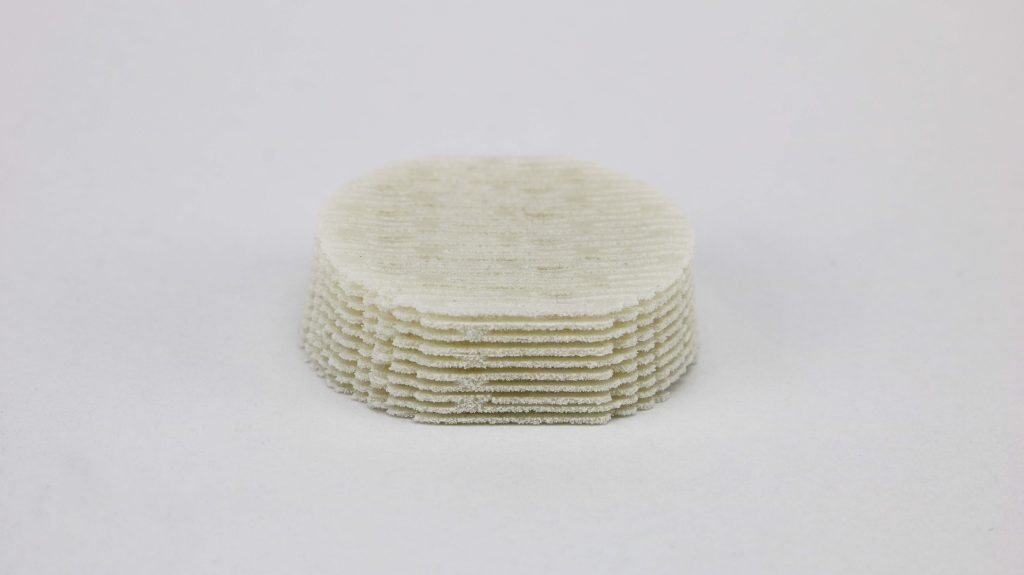
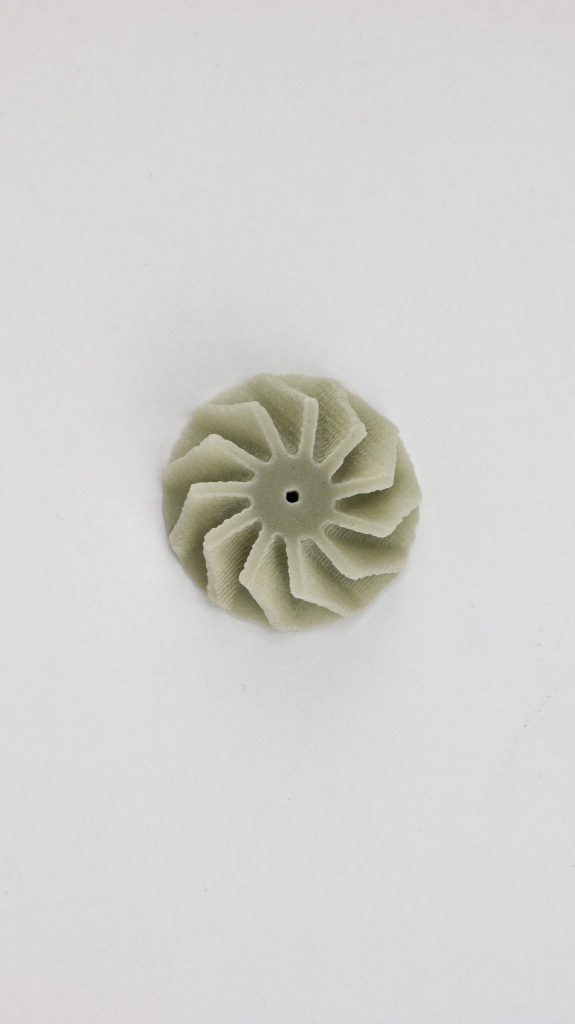
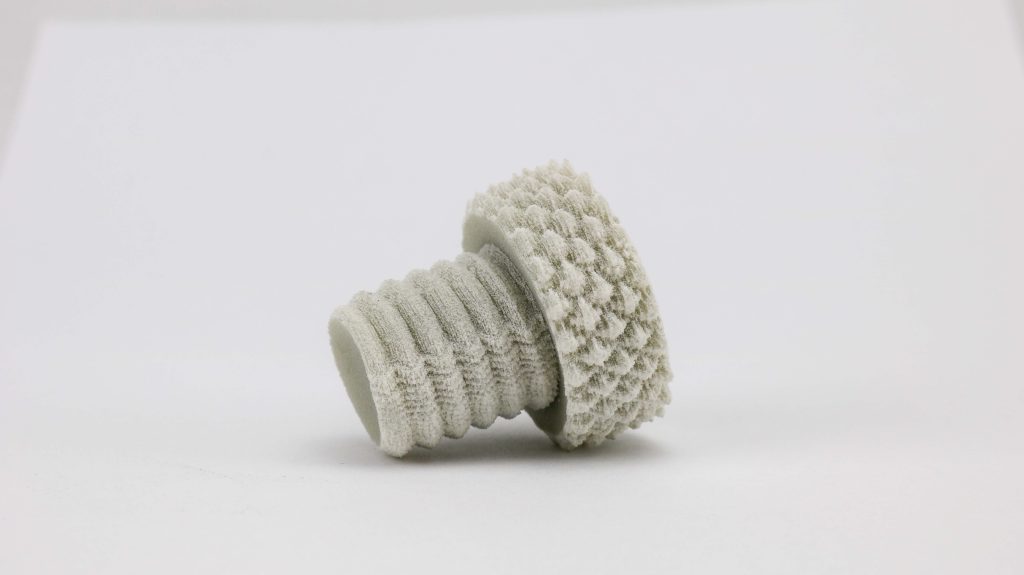
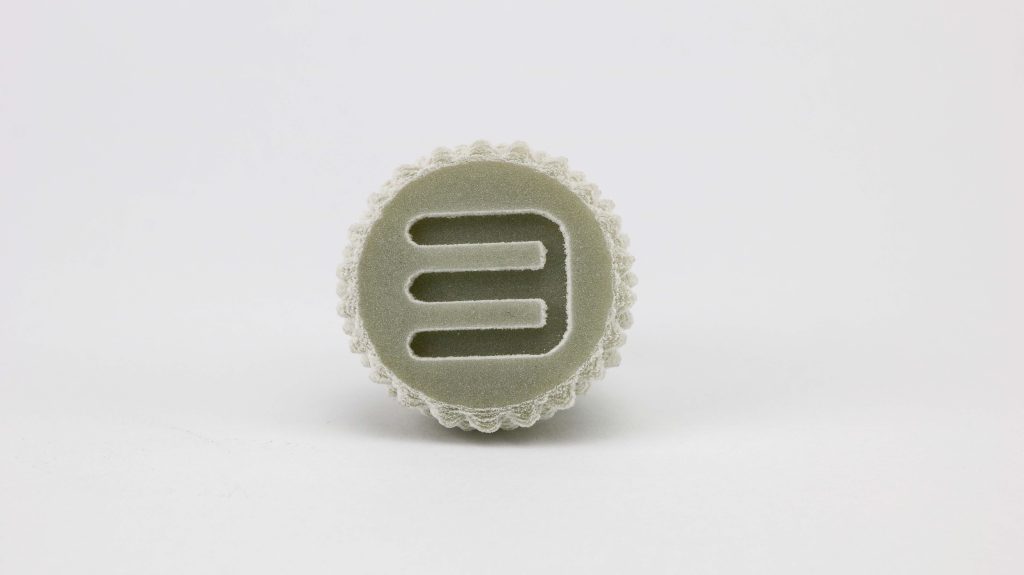
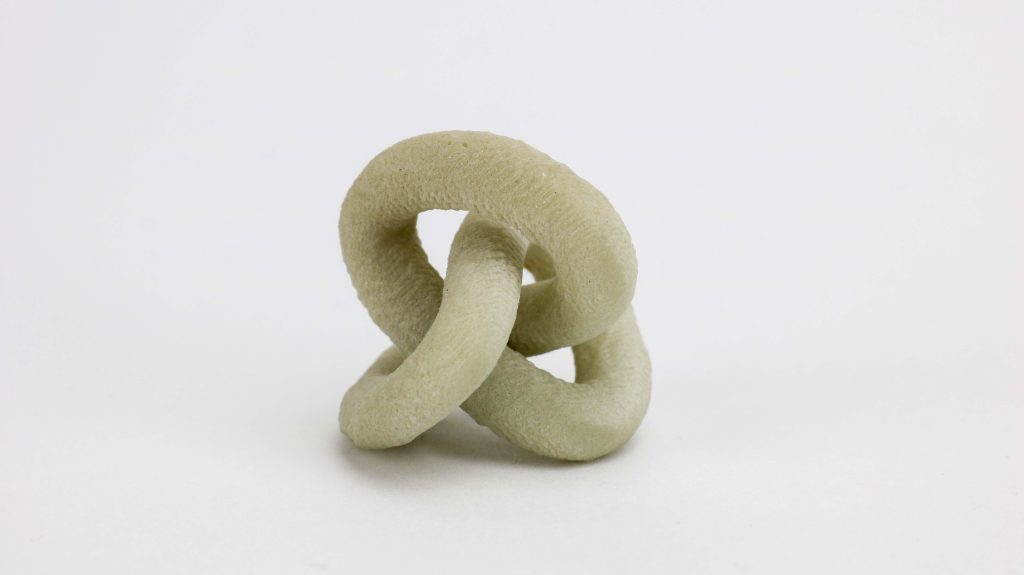
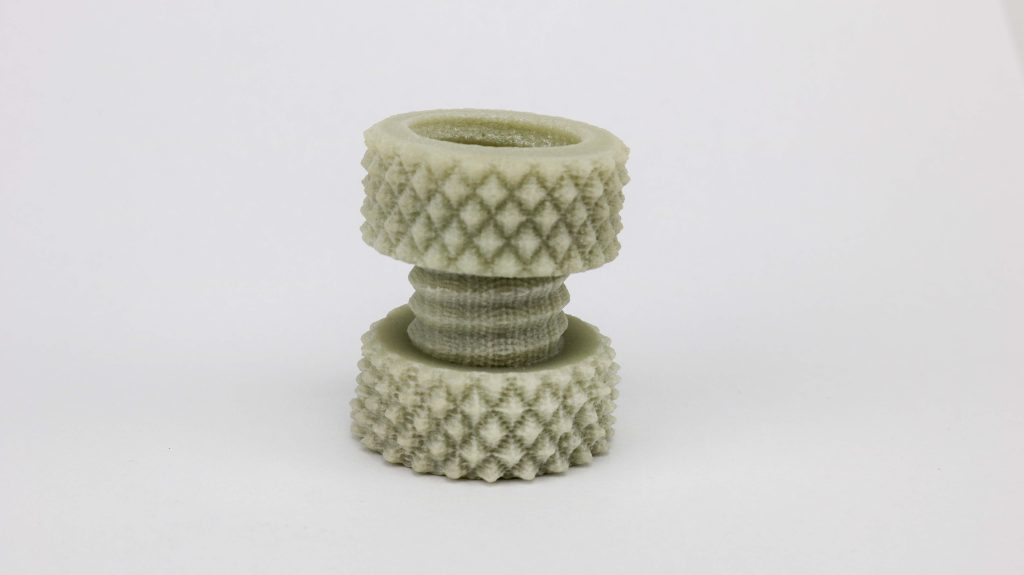
Can this process be applied to other materials?
Yes! By adjusting the process to the specific material used, a wide range of powders is feasible. More specifically the choice of support material and the furnace used will be impacted by the material choice.
This process theoretically works with a wide variety of metals and ceramics or even to produce multi-material parts. The recoater can lay down up to 3 materials simultaneously.
Multi-material disc/plate fabrication was already demonstrated in the past by using this process in combination with SPS/FAST furnaces. The process here is similar with the exception that no support powder was used. The entire bulk powder is sintered into a disc out of which an end-user part can be machined. This approach could be used to produce cutting inserts, FGMs, or layered structures.
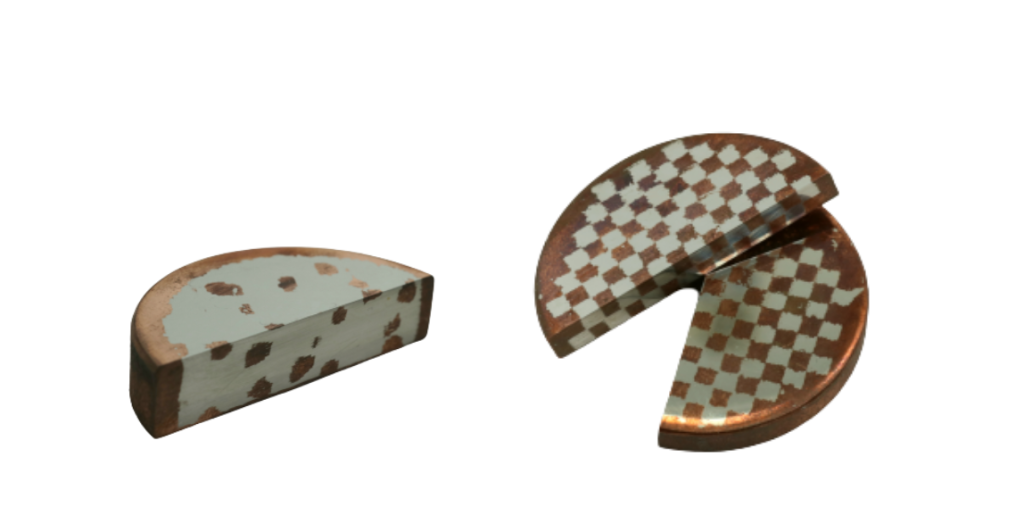
316L + Copper discs densified using Field Assisted Sintering
Speed is a key benefit, and resolution is a limiting factor
This process is incredibly exciting considering the speed at which parts can be produced. No time-consuming laser scanning or de-binding is needed. Even the largest dies can be automatically filled in less than an hour and then transferred in bulk to a furnace for sintering. This process could be very attractive for near-net shaping of all sorts of parts.
One of the limiting factors of this process is that the achievable surface roughness is limited by the selective powder deposition resolution. At the moment this resolution is 300 microns. This results in a relatively rough part surface that will either be accepted as such for the application or will require smoothening through post-processing techniques.
In conclusion, selective powder deposition technology can be used to create intricate glass objects using alumina as a non-fusible support powder. The process involves depositing the powder in a die and selectively melting it layer by layer. This technique can also be applied to other materials such as ceramics and metals, making it a versatile tool for additive manufacturing. As the technology continues to advance, we can expect the powder deposition resolution to improve allowing for the creation of even more complex and detailed objects with this very cost-effective process.