Field-assisted sintering (FAST), also referred to as Spark Plasma Sintering (SPS), is a powder metallurgy technique used to produce dense and high-performance materials by applying pulsed electric current and pressure to a powder compact. The process involves placing the powder compact between two electrodes and applying a pulsed electric current while simultaneously applying pressure. The current causes rapid heating and sintering of the powder particles, resulting in a dense and uniform material with improved mechanical, electrical, and thermal properties.
Tricky mold-filling process
Filling the molds for FAST/SPS can be tricky due to the nature of the powder-filling process. When loose powder is poured into a mold, it can be difficult to achieve uniform packing and avoid voids or defects in the final part.
The powder particles can settle unevenly, resulting in areas of low density or voids in the final part. This can lead to reduced mechanical properties and performance, as well as decreased consistency in the parts produced.
In addition, powder flow and compaction can be affected by several factors, such as particle size distribution, surface area, and powder morphology. These factors can affect the packing density of the powder bed and lead to non-uniform heating and sintering during the FAST/SPS process.
Selective Powder Deposition (SPD) as a way to overcome this challenge
SPD, as developed by Aerosint, is a way to precisely deposit a layer of powder onto a substrate. This technology selectively deposits multiple powders to form a single layer containing at least two materials.
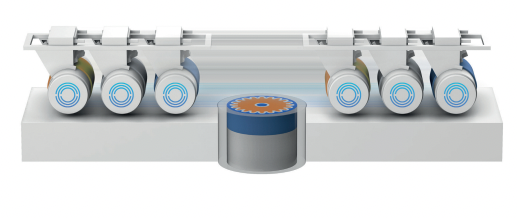
By using selective powder deposition, the powder can be distributed more evenly in the mold, ensuring a higher packing density and reducing the occurrence of defects. This can lead to parts with improved mechanical properties and consistency.


In addition, selective powder deposition can also be used to introduce additives or reinforcement materials to the powder bed, further enhancing the properties of the final part. For example, metal matrix composites can be produced by selectively depositing reinforcing particles in the powder bed before sintering.
Overall, selective powder deposition can help to overcome some of the challenges of traditional powder filling methods in FAST/SPS and improve the quality and performance of the final part.
You can find more information about the Aerosint die filling machine here.